1、技术壁垒
激光器行业属于典型的技术密集型行业,激光器作为激光设备的核心器件,涉及光学与光电子学、自动控制、机械设计与机械工程、材料科学、热力学等学科领域,是多学科相互渗透、交叉融合而成的高新技术产品。本行业必须掌握激光核心技术并建立与之兼容的光路、电路、机械、软件方案和技术参数体系,对新进入者形成较高的技术壁垒。此外,即使产品研发取得成功,实现产业化还需要生产工艺、原材料配套、技术体系、元器件参数配套、质量控制标准等行业经验的长期探索、修正和积累,保证产品质量稳定可靠。
如果激光器生产厂家同时还掌握激光器核心光学器件的技术工艺,了解激光器特定指标对光学器件制造的要求,则可以更好地提升激光器性能、加速新产品的研发效率。通过器件与激光器的不断融合与技术迭代,能够形成短期内难以复制的技术壁垒。
目前全球高端光纤激光器生产技术主要被 IPG、SPI 等少数企业掌握,国内仅有发行人、武汉锐科等少数几家本土企业实现量产。
2、成本控制与规模效应壁垒
在光纤激光器成功国产化之前,我国光纤激光器市场一直为跨国巨头所垄断,在与外资品牌竞争时,国内企业必须在满足客户对产品性能和质量要求的前提下,有效控制成本,以更高的产品性价比,打开市场突破口并赢得客户。因此,成本控制能力成为进入本行业的主要壁垒之一。激光器是高新技术产品,高昂的研发支出会抬高单位产品投入;同时在新产品推广初期,元器件采购不具有规模优势,生产标准化程度较低导致产品良率不高,故产品定价较高,不利于市场拓展。因此规模生产企业的低成本优势限制了新的行业进入者。
3、人才壁垒
激光器行业属于技术密集型和知识密集型行业,由于激光器在国内产业化的时间相对较短,有丰富行业经验的从业人员较少,具有行业经验的技术及管理人才,尤其是高端人才仍较为紧缺。另一方面,培养一名专业激光人才的时间成本较高,国内高端激光人才不足的局面短期内难以解决,较高的人才培养成本进一步抬高了行业进入壁垒。4、品牌壁垒
激光器是下游激光设备的关键部件,对设备主要性能指标和运行稳定性具有重要影响。激光设备生产商倾向于采购性能突出、运行稳定可靠、运行成本低、售后服务好的激光器,良好的品牌形象、稳定的运行记录、良好的加工效果、快速的市场响应能力和优质的售后服务均是激光器生产企业获取客户资源的必要前提。随着国内激光行业的发展,激光器与下游激光设备生产商已逐步形成相对固定的战略利益联盟,深入渗透特定应用端的优势激光设备生产商在加速发展的过程中与品牌激光器企业形成了销售、渠道、售后深度融合,更有利于品牌激光器企业抢占市场份额。而良好的品牌形象需要企业经过长期的市场积累逐渐形成,短期内很难获得,因此良好的品牌影响力构成行业的进入壁垒。
二、影响行业发展的有利和不利因素
1、影响行业发展的有利因素(1)国家产业政策的支持
激光器行业一直是我国重点鼓励和大力支持发展的行业,享受多项政策优惠。《国家中长期科学和技术发展规划纲要(2006-2020 年)》将激光技术列为重点发展的八项前沿技术之一,并在科技投入、金融、税收等方面提供支持。《“十三五”国家战略性新兴产业发展规划》、《“十三五”国家科技创新规划》、《国家增材制造产业发展推进计划(2015-2016 年)》等国家政策、发展规划均强调重点支持激光产业的发展。为提升我国制造业竞争力,推进产业转型升级,国务院于 2015 年 5 月发布了《中国制造 2025》,提出要加快制造业绿色改造升级,加快应用清洁高效铸造、锻压、焊接、表面处理、切削等加工工艺,实现绿色生产。激光技术在制造加工工艺方面高效、清洁的独特优势,将助力国家推动绿色生产,必将受益于国家产业转型升级。
参考中国报告网发布《2018-2023年中国激光器产业市场现状规划调查与投资前景规划预测报告》
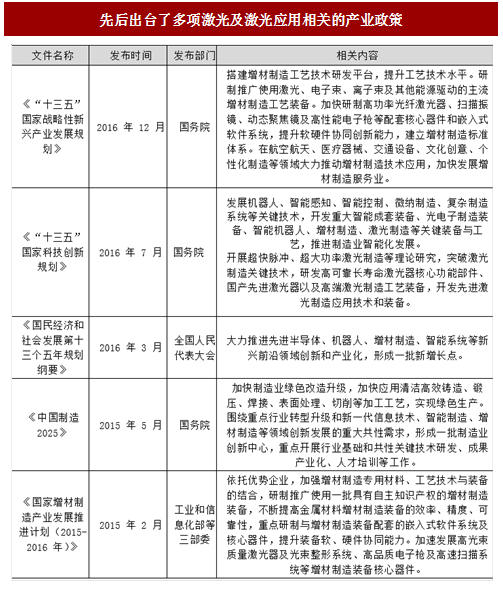
(2)我国进入激光技术大面积推广应用时代
从全球激光产业发展历程看,发达国家在汽车、机械、电子、航空、冶金等领域推广使用激光加工技术,已基本完成激光技术对传统加工技术的替代,进入 “光加工”时代。经过近几年的快速发展,我国激光产业已初具规模,形成数个激光产业集群,但市场渗透率与发达国家相比还存在较大差距,尤其是在大功率激光技术应用方面。在国家产业政策的推动下,汽车制造、机械加工、航空航天、船舶等领域有望大面积推广使用激光技术。下游应用领域的拓展将进一步促进我国激光产业的健康持续发展。(3)日益成熟的配套产业为激光器行业的发展提供产业链支撑
华中地区、珠三角地区、长三角地区、环渤海地区逐步发展成为全球重要的激光产业基地,分布大量激光企业、激光研究机构和应用工厂,逐步形成激光基础材料、激光光学器件、激光器、激光器配套件、激光应用开发系统、公共服务平台等环节构成的较完整的产业链条。日益成熟的产业配套体系为我国激光器行业发展提供了原材料和市场支撑,有利于促进本行业健康发展。(4)新兴应用领域快速发展
激光加工技术是一种应用定向能量进行非接触加工的新型加工技术,与传统接触式加工方式有本质区别,可与其他众多技术融合、孕育出新兴技术和产业,将对许多传统加工产业产生重大冲击。将激光技术、自动化技术、人工智能技术等有效结合而成的 3D 打印技术就是其中之一,作为一种全新的制造技术其应用优势突出,尤其是在零部件结构高度复杂的尖端科技领域,比如航空发动机、火箭飞行器、汽车发动机等的制造。随着 3D 打印材料和打印设备价格的下降,3D 打印市场有望迅速扩展,成为重要的加工手段。随着皮秒、飞秒激光技术的逐步成熟和产业化,激光将更广泛地应用于蓝宝石、特种玻璃、陶瓷等脆性材料的精密加工,支撑半导体、消费电子等产业的发展。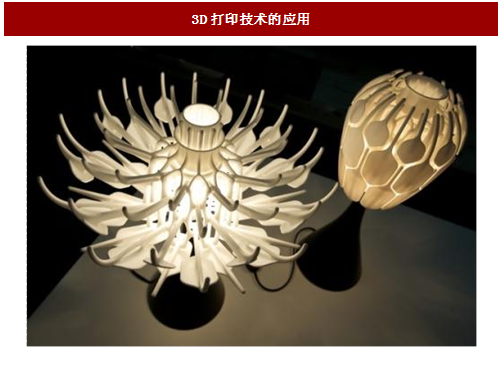
2、影响行业发展的不利因素
(1)我国激光技术水平整体较落后
我国由于激光产业化起步较晚,在高端核心技术方面与发达国家存在较大差距,部分关键器件仍然依赖进口。高端核心技术的落后成为我国激光产业发展的瓶颈。目前,以发行人为代表的本土激光器生产商通过多年的自主研发,逐步向高端激光技术领域探索,并在部分领域取得了突破。但与国际先进激光技术相比,还存在一定差距,比如在大功率光纤激光器领域,IPG 早在 2009 年便研发出万瓦级光纤激光器,而我国首台万瓦级光纤激光器诞生于 2013 年且至今未实现工业化生产。加快前沿技术研究及高端产品国产化是提升我国激光产业竞争力的关键。(2)高端人才缺乏,制约行业发展
目前我国高端光纤激光技术人才相对缺乏。光纤激光器是光、电、机械、计算机、材料等多学科领域知识的交叉融合,产品精密度高,行业技术更新速度快,要求行业技术人员既掌握相关理论知识,又具备较高应用开发能力。目前国内高校培养的激光专业技术人才数量有限,应用研究能力较弱,不能很好满足行业快速发展的需要,存在较大人才缺口。专业人才的缺乏在一定程度上制约了我国激光技术和激光产业的发展。(3)企业规模较小、研发投入能力有限
光纤激光器行业属于技术密集型行业,专业人才的培养和新产品的开发投入较大,只有规模企业能够持续通过人才培养投入和研发经费投入,不断提升产品质量,丰富产品线以满足客户需求。我国本土激光器产业起步较晚,光纤激光器行业直到 2000 年以后才逐渐发展起来。由于发展历史较短,企业规模普遍较小,技术水平较低,抗击风险能力较弱,在人才培养和研发投入方面能力有限,继而影响到行业的整体发展水平和速度。为扭转我国高端激光器长期依赖进口的不利局面,提高我国激光产业在全球的竞争力,激光器行业亟需增加研发投入,加快关键核心技术的攻关,实现核心器件自主配套,以满足国内外对高端激光产品的需求。
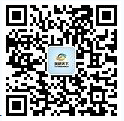
【版权提示】观研报告网倡导尊重与保护知识产权。未经许可,任何人不得复制、转载、或以其他方式使用本网站的内容。如发现本站文章存在版权问题,烦请提供版权疑问、身份证明、版权证明、联系方式等发邮件至kf@chinabaogao.com,我们将及时沟通与处理。