从2016 年国内外主要的多晶硅企业的生产成本分析可以看出,国内产能的新兴厂商在生产成本方面具备显著优势。目前全球多晶硅产能前三位为德国瓦克,江苏中能以及韩国OCI,合计产能约20 万吨,占全球产能比重为45%左右。根据企业披露的成本数据,德国瓦克和韩国OCI 的生产成本折算成人民币为近100 元/千克,江苏中能的生产成本预计也在75 元/千克以上。而国内目前产能居于第二梯队的四川永祥、新疆大全和新特能源的生产成本均在75 元/千克以下,四川永祥60 元/千克的生产成本处于行业最低水平。在2017 年上半年,四川永祥、新疆大全和新特能源均在原有产线的基础上进行了技改和扩建,利用较少的投资金额快速扩张了产能,预计2017 年三家企业的生产成本能够进一步降低。

参考观研天下发布《2019年中国多晶硅铸锭炉行业分析报告-产业规模现状与未来规划分析》

为何新兴厂商能够取得后发优势,在成本上大幅领先行业龙头企业?可以从多晶硅生产成本的细分构成进行分析。多晶硅的生产成本主要包括能源电力、原材料、折旧和人工四部分。因此多晶硅生产成本的降低无外乎减少能源消耗,降低原材料成本,降低初始投资和节约人工成本这四个方向。


以具有代表性的全球产能龙头德国瓦克和生产成本位居领先地位的国内企业四川永祥进行成本构成的对比分析,(德国瓦克可能在能源动力与原材料的构成中与国内企业分类略有不同,构成差异较大。)从成本构成占比分析,差异最大的为人工成本,德国瓦克人工成本占比在30%以上,远高于四川永祥披露的人工工资6.6%的占比,另一家海外龙头OCI的人工成本占比同样在30%以上。其他成本构成从百分比角度考虑存在一定差异。从绝对值测算,以德国瓦克生产成本100元/千克,四川永祥生产成本60元/千克测算,可以得出瓦克折旧成本约19元/千克,四川永祥折旧成本约15元/千克,通过技改扩产至2万吨后目前永祥折旧成本已经降至10元/千克左右。德国瓦克能源动力和原材料合计成本的绝对值约为44元/千克,四川永祥这两项的合计则为40元/千克,两家企业基本保持一致。因此目前国内新兴厂商企业与海外龙头企业相比,最大的优势在于人工成本,其次则是折旧成本。
从人工角度分析,多晶硅行业之前主要集中于欧美发达国家,国内的人工成本与发达国家相比,具备较强的竞争力,这是国内整体制造业对于发达国家的比较优势,优势能够维持较长时间。
从折旧成本角度分析,每年的折旧金额对应的是生产线初始投资成本,随着技术的成熟和生产工艺的完备,多晶硅生产线的投资成本经历了快速下降的过程。目前产能前三的龙头企业进入行业较早,而早期的产能建设单位投资远高于现在的水平。由于多晶硅产线初始投资高,折旧在生产成本中占较大比例,前期高投入的产线对于整体折旧成本会形成一定的负担,拉高企业整体生产成本。2011年之前,国内多晶硅生产尚处于起步阶段,设备均由海外厂商生产,投资金额基本处于50亿元/万吨以上的水平,随着国内多晶硅行业的逐渐成熟,设备国产化比例的提升,多晶硅产线的投资成本持续下降,目前多晶硅的初始投资金额已经降低至约15亿元/万吨的水平,具备优秀技术积累和部分自行设计能力的企业已经将初始投资降至10亿元/万吨左右。初始投资成本的大幅下降最受益的是具备技术优势,同时原有产能有限的新兴厂商,能够通过快速扩产形成具备较强成本竞争力的产能,低折旧成本在面对行业竞争时更具优势。

在能源电力领域,想降低电力成本无外乎到低电价地区建厂和降低综合电耗这两种方法。国内多晶硅企业的能耗成本占比平均在40%左右,其中电力占据核心地位,而电价的高低在全国范围内差距较大,因此到低电价地区建设生产多晶硅是控制生产成本中弹性较大的部分。从国内多晶硅产能分布情况来看,行业整体产能不断向中西部低电价地区集中。新疆大全2014 年就将全部多晶硅产能由重庆万州搬迁至新疆石河子,江苏中能也计划讲2 万吨产能由徐州搬迁至新疆,同时计划在新疆新建4 万吨产能。四川永祥2018 年新建的5 万吨产能分别位于四川乐山和内蒙包头,可以利用四川的水电资源和内蒙的煤炭资源优势。随着电改逐渐放开,未来中西部电力供给过剩的地区的电价还存在进一步下降的空间,多晶硅生产成本中电力成本将继续下降。
虽然低电价对于多晶硅企业具有强大的吸引力,但是多晶硅生产也需要各种因素综合考虑。首先,在西北地区建设生产基地需要考虑气候条件的影响,西北地区的高风速和冬天的低温对于生产线的钢材要求提升,在新疆建设多晶硅厂的初始投资成本高于内地20%左右。其次,厂房建在过于偏远的地区会降低对于核心技术人员的吸引力,更容易造成人员流失,难以打造稳定的团队。产业集群效应也是重要的影响因素,在同一个工业园区中,多晶硅企业所需的部分蒸汽、氯气等可以与部分工业企业协同,降低生产成本。多晶硅制造与下游硅片企业贴近,能够节约运输成本,并与下游客户形成良好的协作关系。因此,电价的高低不是多晶硅生产选址唯一需要考量的因素,并不是说在新疆建厂的成本优势一定优于其他地区,需要进行综合考量后才能得出最优选择。

除了寻找便宜的电以外,另一个降低电力成本的要素就是降低生产的综合电耗。多晶硅生产电耗中最主要的环节在于还原电耗和冷氢化电耗。根据光伏行业协会的数据,国内目前多晶硅行业的平均还原电耗为52kwh/kg,冷氢化电耗为9.35kwh/kg-Si,平均综合电耗为80kwh/kg。根据光伏行业发展线路图中的规划,至2025 年多晶硅生产的平均综合电耗有望降至57kwh/kg,存在27%的下降空间。
除了电力外,多晶硅生产环节的其余能耗包括余热、蒸汽,在原材料领域主要包括硅耗量、水耗、氯气消耗等,未来各环节的成本均存在稳定的下降空间,降成本是长期持续的过程。

国内部分具备技术优势的多晶硅企业在各项能源和原材料消耗中已经实现远优于行业平均的领先水平。如四川永祥自2015年3月底完成四氯化硅冷氢化节能技改以来,多晶硅产量稳步提升,通过持续的研发,还原效率不断提升,单位电耗不断下降,这也是四川永祥生产成本业内最低的重要原因。2016年四川永祥多晶硅生产的综合电耗已经降至67度/千克以下,处于业内领先水平。在建的新产线生产效率将进一步提升,综合电耗有望降至60度/千克以下,未来成本优势将更加凸显。


从四川永祥电耗数据分析,在冷氢化技术方面公司拥有远超行业平均的优势。四川永祥冷氢化电耗约为3.6kwh/kg,转换效率达到25%;而目前行业平均的冷氢化电耗为9.35kwh/kg,平均转换效率在18%-20%左右。在还原电耗方面,公司平均还原电耗约为44kwh/kg,优于行业平均52 kwh/kg。行业内还原炉主要采用美国GTAT的技术,能耗相对较高,而四川永祥通过强大的技术实力,将还原炉的海外技术结合了自身的改进,实现了能耗稳定的情况下对多晶硅品质的提升。在还原电耗接近的情况下,四川永祥产出的多晶硅致密料比例远高于同行,更能满足单晶客户的需求。
通过良好的技术积累和学习,国内多晶硅新兴厂商的技术已经接近于海外的行业龙头,在扩产时则不用受原有产能的拖累,能够快速降低生产成本,拥有显著的后发优势,预计未来拥有技术和资金优势的国内新兴厂商扩产进程将持续,优秀的企业能够最终跻身于行业内全球第一梯队。
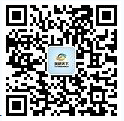
【版权提示】观研报告网倡导尊重与保护知识产权。未经许可,任何人不得复制、转载、或以其他方式使用本网站的内容。如发现本站文章存在版权问题,烦请提供版权疑问、身份证明、版权证明、联系方式等发邮件至kf@chinabaogao.com,我们将及时沟通与处理。